Cost saving advantages of floating ball steam traps Ayvaz flash tank system
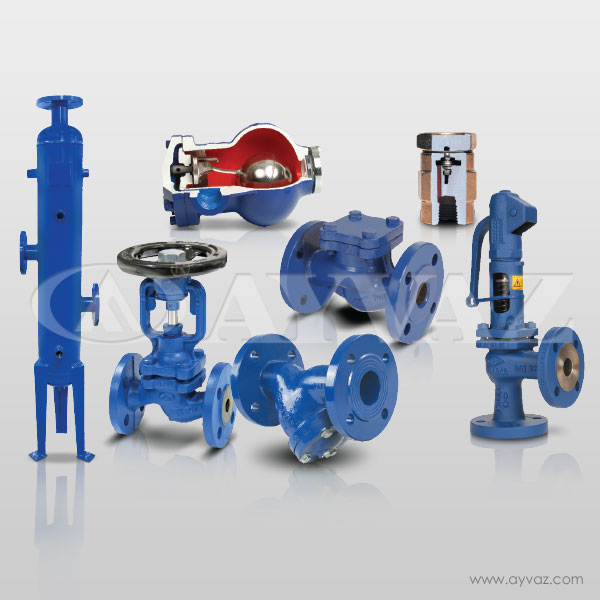
Notes on the selection of flash tanks: saturated steam evaporating from the heat transfer surface is converted to condensate at the same pressure. The enthalpy of saturated water at a pressure of 1 bar is 505 kJ / kg. If the condensate pressure at 6 bar is reduced by 1 bar, the heat release is 697-505 = 192 kJ / kg. This heat evaporates some of the condensed water into steam, called flash steam.
Getting Flash Steam
When the water is heated at atmospheric pressure, the temperature rises to 100 °C.
The absorbed heat does not raise the temperature, but it converts the water into steam.
The heat absorbed by water during the temperature rise to the boiling point is called "sensible heat" or "saturated liquid heat". At the same temperature, the amount of heat required to convert boiling water into steam is called "latent heat".
The heat required to raise the temperature of 1 kg of water by 1 °C at atmospheric pressure is 4186 kJ.
At a steam temperature of 8 bar, the saturated liquid temperature of the condensate is 721 kJ / kg (saturated steam table).
If the above condensate leaks into a 2 bar tank, its calorific value (saturated liquid temperature) drops to 504 kJ / kg.
That is, excess condensate releases heat 721-504 = 217 kJ / kg. The percentage of condensate converted to steam is calculated as follows:
% flash steam = (Q1-Q2 / q) x100 Q1: Heat enthalpy of high-pressure saturated water at the inlet end of the trap Q2: Heat of low-pressure saturated water at the outlet end of the trap q: Hydrophobic The latent heat of the low-pressure saturated steam at the outlet of the valve is % flash steam = (721-504/2201) x100 = 9.6% means that if the condensate is 3000 kg, the flash steam = 3000x9, 6% = 288 kg.
Flash tanks are used to separate flash steam from condensate.
In order to make the flash steam flow to the upper end outlet at the correct speed, the diameter of the steam tank must be appropriate. The speed is about 3-5 m/s, and water droplets can flow into the bottom of the tank at this speed. To increase efficiency, the condensate inlet of the flash tank should be installed in the lower third of the tank. The diameter of the flash tank should be such as to allow condensate to pass without entering the steam stream.
If the pressure difference between the high pressure inlet end and the low pressure outlet end is small, the amount of steam is less than the amount of condensed water. Selecting the flash steam outlet pipe diameter based on speed will result in a smaller flash tank. Therefore, the diameter of the flash tank must be chosen to be twice the size of the flash steam outlet pipe.
Selection of flash tanks
1 - Requires the largest amount of condensate to get the most flash steam.
Therefore, the steam trap capacity must be carefully selected, taking into account the condensate back pressure. In addition, it should be noted that if the temperature control valve is used in the system to close it, the pressure will drop.
2- The steam usage of the flash system must be equal to the amount of flash steam.
When flash steam is missing, steam can be supplied through the pressure drop across the high pressure steam line. If there is excessive flash vapor, excess steam must be drained. In addition, since there is no need to use flash steam for heating in summer, no heat recovery system is required.
Therefore, the amount of flash steam required must be prepared in advance.
3- The system using flash steam is preferably close to the high pressure condensate outlet, because the delivery of low pressure condensate requires large diameter pipes, which increases investment costs and heat losses on large diameter pipes Will reduce the efficiency of the flash tank.
Low installation and equipment costs
Compact design, save space
Built-in filter
Uniform wear on the surface
There is a low probability of a single moving part failing
Low maintenance costs
Good resistance to water hammer
Action
When the steam trap is cooled, the exhaust valve is fully open to continuously discharge the initial air. As the condensate enters the steam trap, the float rises, causing condensate to drain from the valve port and condensate and air from the valve port. Once all of the initial air and condensate have been drained, the equipment connected to the steam trap will reach the operating temperature.
In this case, the amount of condensate drops, but the temperature rises. The steam enters the trap with the condensate, and the high temperature condensate heats the exhaust valve and closes before the steam leaks. The float can be adjusted automatically based on the condensate flow rate. In order to prevent steam loss, the discharge valve is always kept below a certain water level, and metal-to-metal sealing measures are taken.
If draining condensate from the drying drum, add a bypass line to the bonnet to prevent steam locks from occurring. The purpose of the bypass line is to discharge the steam before it enters the trap.